Phoenix 3D Printing is creating a physical object using layer-by-layer fabrication. This method is commonly used to create product prototypes.
This is also known as rapid prototyping. It allows designers to quickly turn their ideas into models that can be observed for form, fit, and function.
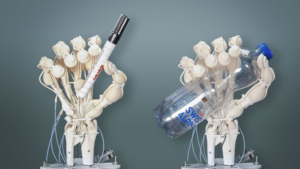
The first step is to design your model using a program like Tinkercad. Then, you must convert the file into a format the printer can understand, called slicing.
Rapid Prototyping
Rapid prototyping is an important part of product design and development, and 3D printing is revolutionizing the industry. It allows companies to turn ideas into realistic proof-of-concept models quickly, advance these concepts to high-fidelity prototypes that look and work like final products, and guide products through a series of validation stages toward mass production.
The process starts with designing a product in computer-aided design (CAD) software. Then, the design file is sent to a 3D printer that builds up layers of material to create the physical prototype. The printer uses computer-controlled technology to determine how each layer should be printed, how much material to use for each section of the prototype, and the dimensions of the finished prototype.
When the first iteration of a prototype is complete, designers can use it to test out functionality and gather feedback from users. This allows designers to iterate and refine designs, which can reduce the time it takes for a product to go from concept to market.
Using 3D printing, designers can also develop high-quality, accurate, and durable prototypes for the product development phase. This can help speed up the product design and development process, which translates to higher productivity for companies.
Additionally, 3D printing offers more versatility than traditional manufacturing techniques. For example, with machining or injection molding, creating a prototype requires the creation of costly tools and molds. However, with 3D printing, the printer itself serves as the tool and mold, which can save businesses valuable time and money.
Having a physical prototype also helps to facilitate communication and collaboration among team members. It enables teams to discuss ideas and feedback in ways that are not possible with 2D drawings. It can also enable a company to show off a new product or innovation to potential investors, clients, and partners.
The most important advantage of 3D printing for rapid prototyping is its ability to reduce the time it takes for an idea to move from concept to delivery. This can drastically improve a company’s business model by cutting months or even years off the time it takes to bring a new product to market.
Rapid Manufacturing
Before 3D printing, engineers were limited to hasty foam mockups or intricate clay models crafted by skilled artisans. These costly and labor-intensive methods could only yield one prototype iteration at a time, and resulted in longer lead times between design cycles and final product approval.
Today, affordable desktop and benchtop 3D printers allow engineers to quickly iterate between digital designs and physical prototypes. This enables rapid changes to the size, shape and assembly of products based on real-life results from testing and analysis. This iterative process enables businesses to improve their products faster than their competitors.
In addition to prototyping, 3D printing also offers a full range of manufacturing services, including the production of functional prototypes and finished components. This includes selective laser sintering (SLS) and stereolithography (SLA), which utilize high-powered lasers to heat and bond particles of a versatile selection of powders into solid, works-like or engineering prototypes. This high-speed method of creating complex parts produces exceptionally strong, highly accurate and dimensionally precise components that are ideal for rigorous tests and end-use functionality.
Engineering prototypes are critical to the product development process, serving as a bridge between design and engineering and communicating production intent to tooling specialists in later stages. They are used for lab-based user testing with a select group of lead users, to demonstrate production intent during the first sales meetings and as a tool for generating a detailed product specification that is used by the factory in mass production.
Using 3D printed prototyping, engineers can verify the fit and function of a prototype before investing in expensive and time-consuming tooling. This reduces the risk of expensive mistakes that would otherwise be costly to correct, and speeds up the process of delivering the final product to market.
A new breed of ‘print-shops’ is emerging across the globe, where entrepreneurs can rent 3D printers by the hour or day to create low-risk concept models and proof of concepts. These local print-shops enable entrepreneurs to get real-life feedback from users and validate their ideas before moving into full scale production, eliminating the need for costly machining and injection molding.
Additive Manufacturing
Additive manufacturing (AM) is a process used to translate virtual solid model data into physical models layer by layer. It can be used for the fabrication of a wide range of materials including polymers, metals, and ceramics.
AM allows designers and engineers to turn CAD designs into prototypes and end-use parts within hours. This dramatically cuts production and testing lead times and enables companies to bring new products to market more quickly. For example, the Airbus AMRC turned to 3D printing to rapidly produce 500 high-precision drilling caps that were needed for testing purposes and cut lead times from weeks to three days.
The benefits of AM are numerous and broad-ranging, from reducing design iterations and improving product quality to increasing flexibility in production and supply chains. In addition, 3D printing enables manufacturers to produce parts in-house that they could not otherwise afford, which reduces costs and the need to rely on third-party suppliers or service providers for complex or critical components.
This new paradigm can create significant competitive advantages by enabling companies to better control their own manufacturing and production processes, as well as protect intellectual property, proprietary innovations, and other trade secrets. Furthermore, the use of AM can help companies avoid the high costs associated with the tooling, fixtures and jigs required by traditional manufacturing and assembly line production.
There are several different AM technologies, which differ in their method of material deposition and the type of materials they are capable of printing. For example, selective laser sintering (SLS) uses a laser to ‘sinter’, or bind together, the powdered material, creating the desired shape.[4] Other AM technologies include material extrusion, vat photopolymerization, powder bed fusion, binder jetting, and sheet lamination.
As the technology progresses and evolves, it is anticipated that it will be used for more advanced applications, such as combining multiple materials, creating organic shapes that cannot be produced by other means, and consolidating assembly parts to reduce weight, improve strength, and enhance performance. It is also possible that it will be incorporated into the design of production equipment and even automobiles.
Additive Design
3D printing has evolved from a rapid prototyping technology to a full production technology. However, this shift has not been without challenges. It is important for engineers to design parts with additive manufacturing in mind. This can help reduce costs, improve functionality, and increase the durability of the part. This is known as Design for Additive Manufacturing (DfAM). DfAM is an engineering design process that focuses on the optimization of a part, assembly, or product to take advantage of the unique traits of additive manufacturing processes. DfAM leverages a number of tools and techniques, including simulation, modeling, and optimization.
The key to designing for additive manufacturing is understanding how the layer-by-layer process works. This allows designers to optimize their designs by isolating geometrically complex features and simplifying them for the additive fabrication process. This reduces print time and cost, improves workflow, and makes it easier to iterate and modify the part if necessary.
In addition to the layer-by-layer printing process, additive manufacturing technologies also enable a more modular and flexible design. By using a variety of materials and the ability to build multiple components in one print run, the possibilities for a final part are almost endless. This flexibility and adaptability can reduce cost, lead time, and complexity, as well as decrease risk in supply chain operations.
Using additive manufacturing, engineers can quickly produce prototypes and small production runs for testing or use in their plants. For example, a part produced with CNC milling that would require five distinct operations, three different cutting tools, and two setups can be created in a single operation with 3D printing. This can reduce the development cycle by weeks or even months, allowing companies to bring their products to market sooner.
Increasingly, industrial companies are using 3D printing to make their production more efficient and responsive. By integrating additive manufacturing into their production processes, they can eliminate the need for spare parts, shorten delivery times, and create a more responsive supply chain. In one case, GE aviation was able to produce a helicopter engine with 16 parts instead of 900, saving them significant time and money.