Whether it’s your own house or you’re considering selling, significant foundation cracks can be a deterrent to potential buyers. Taking the time to understand the process and your options is the best way to prepare.
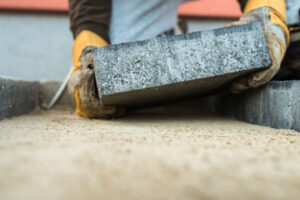
It’s important to choose a contractor who specializes in foundation repair. This is because they have the expertise, equipment, and training needed to perform the job correctly.
Many people get nervous when they notice cracks in their foundation. While some cracks are non-structural and don’t pose an immediate threat to a home’s structural integrity, they still need to be treated as quickly as possible to prevent water leaks and mold growth. For non-structural cracks, you can use a caulk and latex mixture or hydraulic cement to seal the crack. Once the crack is repaired, it’s important to monitor it for new problems and signs of further damage.
Other types of cracks indicate a more serious problem and may require professional repair. Horizontal cracks in a foundation wall usually indicate hydrostatic pressure from water and soil pressing against the foundation walls. This type of crack can be very dangerous, especially if it’s accompanied by bowing or leaning walls. If you notice horizontal cracks, contact a foundation contractor right away.
Vertical or jagged diagonal cracks in a foundation wall are also a sign of significant foundation settlement and are not normal. Depending on the cause, these cracks could be a result of poor construction techniques during new construction, or they may be caused by a shift in the soil underneath the foundation that puts stress on the foundation. In many cases, these cracks need to be corrected with epoxy injections or carbon fiber reinforcement.
Gaps in a concrete foundation are another common problem and should never be ignored. They can be caused by natural settling or shrinkage of the concrete, but they’re typically not a problem unless they’re very wide or allow groundwater or rainwater to enter the basement or crawl space. When cracks or gaps widen, they’re often caused by differential foundation settlement and need to be fixed with carbon fiber reinforcement or epoxy injection, or piers can be used in severe cases.
When a foundation repair job is done correctly, all of the above signs should be improved or eliminated. The cracks should be closed, doors should work properly again, and gaps or leaks should be repaired. If you’re concerned about your foundation repairs, it’s best to contact the company that performed the work and ask them about their warranty or guarantee.
Water Invasion
Rain and water damage are an inevitable part of life for a foundation, but that doesn’t mean you have to accept the results. If the signs of rain damage are spotted early enough, the problems can often be corrected before they escalate.
The best way to prevent the damaging effects of water intrusion into a foundation is to ensure that proper drainage is in place and that any leaks are repaired immediately. This will help reduce the amount of water that seeps into and around the foundation, and it will also help to keep soil moisture in control.
Water damage to a foundation is often caused by something called hydrostatic pressure. This is simply the force of water pushing against concrete, and it can cause cracking and bowing walls. The amount of pressure will vary based on the season, as rainy seasons or spring thaws can increase the amount of water that comes into contact with a home’s foundation.
It is important to regularly inspect the exterior and interior of a home for any signs of foundation problems, including horizontal cracks that develop from soil expansion. If the cracks in a foundation are not addressed, they can continue to widen and eventually undermine the entire structure of a building.
Crawl spaces and basements are particularly vulnerable to water infiltration, since they tend to be dark, damp areas that attract insects. Unwanted creepy crawlies like termites and mold will love these sheltered environments, and they can easily chew through the wooden components that make up the home’s support system.
In order to prevent these issues, it is important to regularly inspect the exterior and interior for any signs of moisture or pests. If you do notice a musty smell or any cracks in your foundation, it is a good idea to schedule a consultation with a professional to take a closer look at the situation. They can provide advice on the best steps to address the problem and repair any damage. By following this advice, you can save yourself a lot of time and money by taking preventive action rather than waiting until the last minute to call a contractor for foundation repair.
Leaking Pipes or Drainage Systems
When a foundation shifts, it can pull or “shake” drain and sewer lines apart. Over time, these pipes can leak waste and water into the soil. In turn, this can cause the soil to swell and create gaps in the foundation itself. This is why it’s so important to get any leaking or broken pipes repaired as soon as you notice them.
Wet spots or stains on walls, floors, or ceilings are often the first sign of a foundation leak. Leaks can also appear as puddles in the yard or near a home’s foundation. Wet spots can be caused by a variety of issues, including plumbing leaks or flooding from rain or groundwater.
A musty or damp odor is also a sign of a foundation leak, and mold and mildew can quickly grow in areas that are exposed to water. Over time, a leaking foundation can damage support beams, which can lead to uneven or sagging floors inside the home.
If your foundation repairs involve the plumbing system, a plumbing test should be performed afterward to ensure that all leaks are fixed. This is especially important if the plumbing is located close to areas where the foundation lifts or supports the structure.
Plumbing tests can also reveal whether or not the foundation repair has affected the drainage system. For example, a faulty gutter or downspout can lead to the drainage system leaking underneath the foundation of a home, which can saturate the soil and cause a leaky foundation.
A faulty or overflowing septic tank can also cause drainage problems, which are common causes of foundation leaks. If you suspect a septic problem, contact us right away to discuss your options. We can install an interior breakout for repair, which involves taking a portion of the home’s plumbing system out through the foundation and rerouting it to allow for better drainage.
Structural Issues
Foundation issues that go unrepaired will lead to other problems throughout the house. This includes misaligned doors and windows, uneven floors, and even plumbing issues. This is especially true of pier and beam foundations that have pipes weaved through them. As the foundation shifts, these pipes can snap and cause flooding or water damage in other areas of the house.
The key is to catch these issues as soon as possible, and repair them before they cause other structural damage or other safety hazards. If you’re thinking about buying a home with foundation issues, it can be helpful to have a professional perform a thorough inspection before closing the deal. This will help you know whether the problem is worth pursuing or not.
During the inspection, you’ll want to look for signs of structural movement, such as cracks in walls and columns or concrete that is out of level. You may also notice bowed or bulging basement walls, sagging crawl space floors, and seepage in the basement. You’ll probably also see misaligned doors and windows in the upstairs of the house above the affected area.
If the cracks or other issues don’t seem serious, they may be a sign that the home’s foundation can be saved by underpinning and other methods. However, it’s best to have a structural engineer determine the extent of the problem to be certain.
Minor foundation issues may not be worth repairing, but this decision should be made with the assistance of a home inspector and a structural engineer. If the home’s foundation is sinking or has other significant movement, it will require underpinning and other extensive repairs to restore it to its original condition.
If the house’s foundation isn’t salvageable, you may need to walk away from the purchase. This is particularly true if the problem has caused other major damage, such as a sagging roof, severe water leaks, or mold and pest infestation. It’s also a good idea to walk away if the seller won’t agree to pay for the required repairs. Even if you have the funds for the repairs, it may be better to find a new house that meets your needs.